张震威 上海宝钢工业技术服务有限公司
李怀金 山东管理学院 信息工程学院
越来越多的制造业企业正在或计划开展数字化转型,不少企业也都根据企业战略制定了“数字化规划”,不过从形形色色的战略转化出的规划来看,虽然企业将工业物联网作为规划中的一部分,但对其所能产出的功效(价值)、实施的路径(方法)、所需的支持(协同)、物联的环境(基础)等都尚未明确,这直接导致贸然开展工业物联网项目后,企业普遍认为与MES等系统差别不大,项目成果未达到实施目的。就此问题,本文根据数个项目的实施过程及实施后评价,对与工业物联网平台相关的几个问题进行分析,以期后续能查漏补缺,同时也对未来发展做适度展望。
2009年9月,欧盟委员会信息和社会媒体司Lorent Ferderix博士提出:物联网是一种动态的全球网络基础设施,它具有基于标准和互通操作通信协议的自主组织能力,其中物理和虚拟的“物”都具有身份标识,其物理属性、虚拟特性和交互协议可与信息网络无缝整合。
而由我国工程院院士李伯虎先生提出的定义为:物联网是通过识别、感知技术与设备获取物体或者环境的静态/动态信息,再由网络传输通信技术与设备进行信息处理,以此实现虚拟与物理世界的智能化管理与控制的智能化高效能网络。
工业物联网属于物联网的一种特殊应用场景,也符合上述定义。但通过时间线来看这三方的定义,可以发现物联网的实质内容在逐步增加:以MIT定义为例,其主要以物理传感器作为媒介,通过协议采集目标对象的相关信息,此时的“物”主要局限在物理世界中。
Lorent Ferderix博士在MIT的基础上,将“物”从物理世界扩展至虚拟世界中,并明确物理和虚拟的“物”可通过交互协议与信息网络整合到一起。我国李伯虎院士在Lorent Ferderix博士的基础上,重点提出了对“物”的管控具有一定的“智能化”。总体来看,其实就是制造业的“信息化”、“数字化”及“智能化”的三个阶段体现。
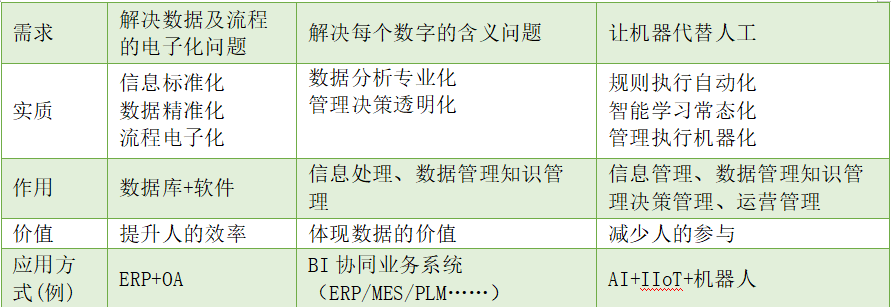
从上述内容不难看出,工业物联网应归类与智能化阶段,要求工业物联网作为AI(虚拟)及机器人(物理)的中间桥梁,实现虚拟大脑指挥物理设备的设想。
如果要实现这样的目标,那么AI就不能单单理解为某一种逻辑算法,而应将AI作为各业务系统的总和,根据知识工程及最优算法输出最经济的业务执行过程,以此来为企业赚取更多的利润。
对于工业物联网而言,根据物联网的定义及发展应概括成:基于以虚拟或物理环境的信息,根据已制定的算法模型,自动出具收益(避免损失或增加利润)最大的系统工程方案。
在制造业中,工业物联网的收益应更为广泛,一般分为行业/产业物联网和企业物联网两种模式。
1.行业/产业的工业物联网
此种物联网更多由政府侧或非营利性组织提出,例如行业协会等。其目的在于避免内耗,提前准备,政策预判等。
在PTC某年度技术大会上,徐州某大型工程机械企业就分享了一则有关于工业物联网的应用实例:在前一年因工程机械行业受累于基建的影响,不少工程机械的设备因采购乏力导致产品滞销,企业决策层正苦恼于库存高企及订单减少的压力,而在此之前已卖出的工程机械设备上已全面加装传感器,通过4G信号传输至企业云端服务器,此时信息化部门的管理层基于此向企业决策层建言,根据目前已卖出的设备开机率来推测,今年年中即可迎来基建及工程机械行业的回暖,同时向决策层提供了开工设备所处于的地域、运行时间等重要信息,最终决策层研判提前应对,顺利完成了当年的经营目标。
从政府侧或行业侧来看,很少能获取第一手可信数据,所以制定出的政策往往不能真正解决问题,而反观工业物联网,其可随时洞察某一个具体行业的现状,并根据近期行业供需的波动,提前预判近期经济形势的变化趋势,继而制定相应的对策,做好全行业/全产业链的协同,为社会赚取更多的收益。
2.企业工业物联网
此类源于企业内部,通过采集企业车间设备(物理)、业务系统的数据(虚拟),为企业搭建决策层、管理层及执行层的一体化业务平台。以业务系统为例:销售人员可以通过IIoT平台实时获取ERP系统中某一产品的可销售库存量,并在客户现场实施调整报价及到货周期,进一步提升竞争优势。
而当库存不足以满足客户需求时,又可以通过IIoT联动MES/APS系统,预测最快的交货周期及交货策略,为销售人员获取订单提供可靠的数据支撑。同理对于采购人员,也可以通过IIoT平台获取近几年内原材料采购价格的波动情况,适度调整采购量。而对于研发或生产人员,可以通过IIoT平台获取PLM/CAPP等系统,制定与企业设备相匹配的生产工艺,并逐年优化,进而提升产品质量,降低不合格品的数量。
而对于企业管理人员,又可以通过设备综合利用率(OEE)来判断产能是否区域瓶颈,并根据业务发展情况制定关停或新购产线的决策。从企业内部推行IIoT的初衷来看,其更偏向于BI式的决策平台,收益的判定更多来源于企业的避损。
3.1实施模式
既然实施工业物联网有上述诸多收益,但如何锁定并落实此部分收益,则是每个企业所面临的难点。从目前实施情况来看,所涉及的主体对象共分3块,分别为设备(物理)、系统(虚拟)、智能(人或算法)。
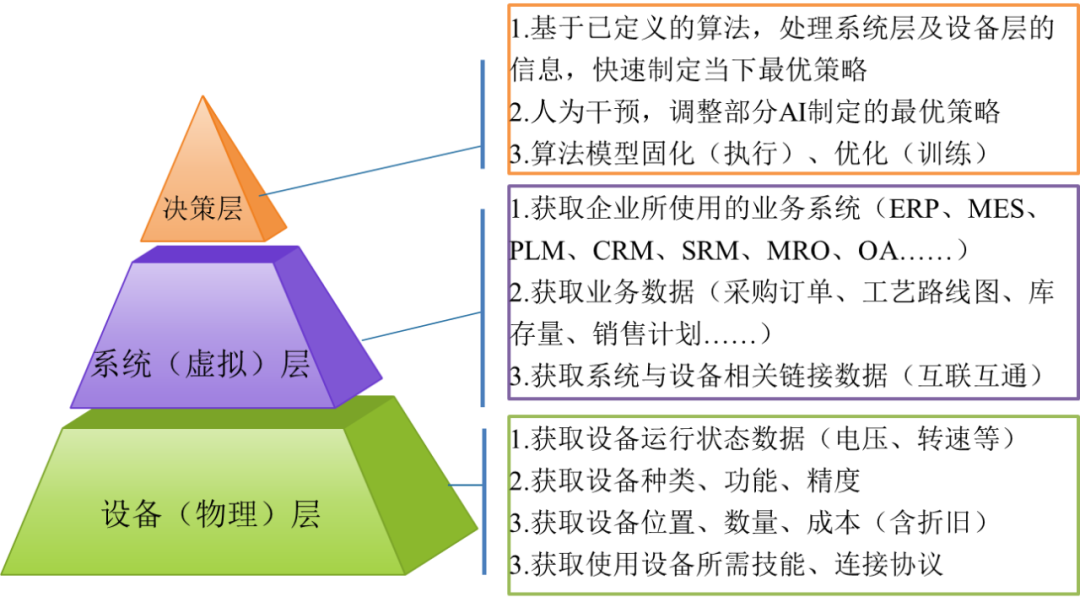
工业物联网若想实现项目目标,则需要根据自身主体及情况,制定合理的实施策略。从广义上来看,工业物联网项目实施就2种主要途径:
1.自底向上(设备-系统-决策)
此种途径常见于企业决策层未制定出清晰的工业物联网平台的应用规划,也没有形成明确的应用诉求及收益点,只从外界获悉了工业物联网平台能力,便准备开展相关项目的实施。此种途径的优势在于:因顶层设计缺乏,为避免考虑不周而引起后续的重复投资,所以在项目实施初,就将企业内部的所有设备登记成册,并根据设备情况,将设备(物理)层的相关数据全部提取出来,待IIoT平台实际使用一段时间后,再将真实的业务需求逐步调整。
而若不采用此种模式,很容易在IIoT上线后业务部门发现提取的信息并非所期望的,在此情况下既浪费了项目投资又难以为企业提供价值。而若将所有数据先期全部采集后,若后续业务发现所要非所得后,可直接进行调整,不用因新数据采集而产生二次投资。
然而对于设备数据全部提取所带来的成本增加,在IIoT系统架构合理规划的前提下,也处于可控可接受的范围。对于数据采集的设备,可按如下划分:
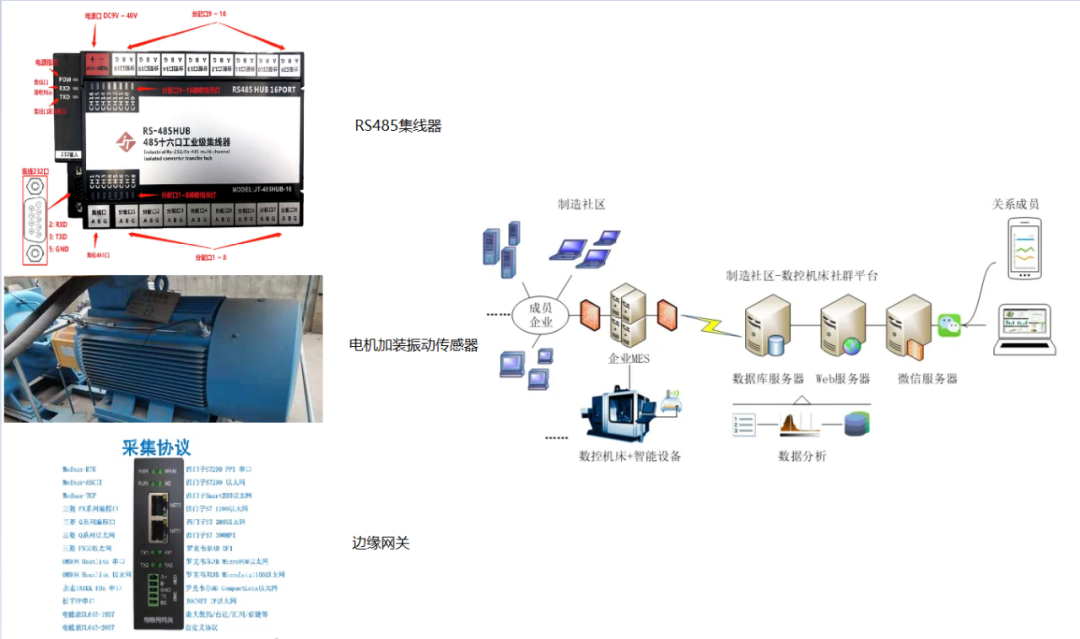
若以自底向上模式计算工业物联网设备采购及调试费用,那么在采集物理量总量不变的情况下,以一次规划完整、数据采集齐备的方式最为经济。
即以自底向上的模式下,应尽可能规划所有所需要采集的物理量或信息,避免后期多次新购对网络及设备产生的影响,也可在后续应因业务需求变化而随时提供相关信息。
同时若考虑大批量采购的优惠,实际一次采购的性价比更优于二次采购。若再考虑二次安装可能带来的对前次安装的改造调整,那么整体实际费用恐怕会更高。
2.自顶向下(决策-系统-设备)
此种模式常见于企业决策层已非常明确业务需求,或者外部咨询公司向公司提供了明晰的、确定的、所需采集的物理量或信息。那么系统层规划及设备层采购按既定决策落实即可。此种模式的优势在于避免了大规模采集所有物理量或信息所带来的浪费,也大为降低因信息量过大而导致的技术难度成倍增加、更避免了因信息量过大导致实施周期过长的问题。
同时此种模式更有利于制造业企业内部推行工业物联网,其原因在于:制造业企业的项目出发点在于通过项目获取收益,而且企业实施项目有预算上限及成本考核,若采用自底向上的模式,虽然也可以实施工业物联网,但靡费甚大。反观自顶向下,当企业决策层指定出信息后,管理层进行拆分及落实就变得更为容易。
3.2新技术使用及理念分析
实施IIoT时,都必须要明确IIoT项目所需要实现的价值,无论实施方式采用哪种模式,只有真正采集到有价值的信息,才能为企业带来收益。根据目前实施的项目,对如下事项进行讨论:
●4G/5G模块
在实施IIoT项目时,常会与ISP(信息服务提供商)合作,首年合作时3家ISP服务商都会开出较为有吸引力的价格,但企业需要仔细计算使用4G/5G信号的RoI,并根据应用场景判断,是否需要接入4G/5G。
i.安全性
车间的设备通过AP网关即可接入4G/5G蜂窝网络,即使在加装硬件防火墙的情况下,依旧难以保证设备数据不泄露,更严重的情况下,车间设备被黑客远程控制,对车间及人员的安全造成威胁。
目前我国是全球受到信息安全威胁最为严重的国家,一旦介入4G/5G网络,在目前的安全形势下,不可能确保设备及人员安全万无一失。在安全的前提下,不建议将可远程控制的设备通过蜂窝网络发布出去。而对于不可远程控制的设备,建议只通过蜂窝网络上传必要的数据,避免对蜂窝网络的流量占用,也降低信息泄露的风险。
ii.使用场景
通过分析4G/5G的性能优势可以大致归纳出相应的使用场景,一般而言借助蜂窝网络(数据高速传输,低延时的优点),在远程会诊、特殊地域信息采集等场景有应用。以远程会诊为例,医生可通过蜂窝网进行跨域远程医疗,对于车间设备故障,设备生产商也可进行跨域维护。特殊地域信息采集场景包括矿场、建筑施工现场、海上钻井平台、气象观测站等。对于制造业企业的车间,一般通过内网进行设备连接,无线也常使用WIFI、Zigbee等实现。
iii.经济性
蜂窝网络的使用费用最主要来自于流量费,ISP一般以首年大幅度优惠吸引用户,次年起恢复正常资费。若以有线网络计费,则费用主要来自于企业网络带宽年费。企业使用IIoT不可能只使用一年,若以5年计,那么以实时传输30台设备参数信息至远程服务器为例,有线网络宽带资费将大大低于蜂窝网络。所以若企业已具备设备维护能力且几乎不需要外部资源支持,IIoT服务器又在企业内部时,则不需使用蜂窝网络。但若企业无设备维护能力,每月都需要外部专家远程运维,或企业为轻资产将数据存放于云服务器时,则可能使用蜂窝网络。
iv.传输性能
从目前公开数据显示,4G信号最大传输速率为100mbps,也就是12.5MB/s。5G信号最大传输速率为10Gbps,也就是1.25GB/s。以华为S5735S-L系列交换机为例,整机交换容量大于336Gbps,所以若服务器与设备采集模块处于同一网络时,内网交换机的传输性能优于蜂窝网络。
当然考虑性能时还需考虑经济性,一般不会对每个传感器都配备无线传输模块,因为按此方式配置则成本将非常高,常规做法是将多个设备的信息传输至某一设备中集中存储,然后对此集中设备安装无线模块,这样统一传输的经济性会更好,即使按此方式,因总流量不变,所以资费依旧比内网要高。且信息集中存放并传输具有一定的瓶颈,一旦超过负载能力,实时效果将打折扣。
●预测性维护/维修
可预测性维护维修是不少企业实施IIoT时的一个需求点,应该说这样的想法很好,很类似上医治未病的理念实践,但IIoT实施完成后,常发现并未实现预测性维修,甚至预测准确性十分低下,究其原因就在于设备故障的发生具有随机性。如同人一样,同一个地域同人种,寿命长短各不一样。
以上海宝钢炼钢厂4cc机组为例,原始设备运维数据由点检员承担,记录每次扇形段更换的时间及炉数。4cc机组设备如下图所示:
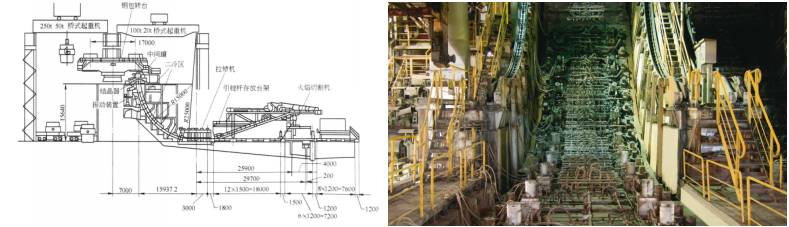
4cc流水线由:1台结晶器(MD)、1台0号段(S0),3台扇形段A段(SA),3台扇形段B段(SB),1台扇形段C段(SC),1台扇形段D段(SD),10台扇形段E段(SE)组成。
运维数据通过点检表记录:
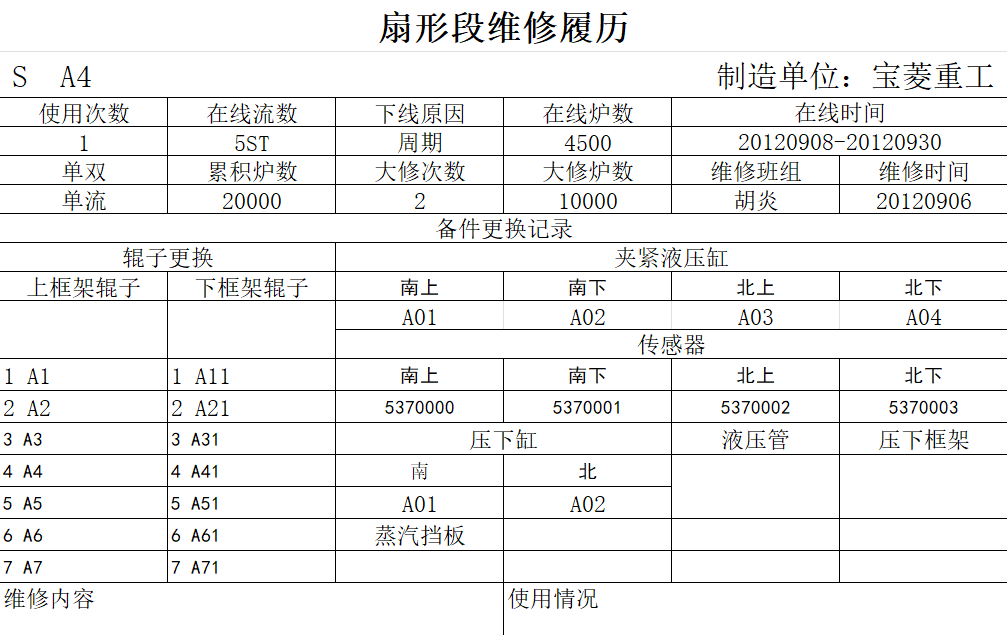
从以往点检记录来看,扇形段的更换炉数飘忽不定,每次连铸设备异常后,对钢坯表面都有一定量的划伤,最终导致钢坯降级甚至报废,对企业日常经营造成损失。所以寄希望于通过IIoT的实施,在连铸设备损坏前,利用浇筑间隔将快损坏的扇形段替换下,以达到减小损失的目的。
实施IIoT后发现预测的准确度很低,没有达到当初的目标,分析有如下原因:
●设备故障的现象与原因是一对多的关系
例如钢坯表面发生划伤,存在多种原因导致:长短辊运行速度不一致,上下段辊子滚动速度不一致,中间支撑破损等。IIoT所采集的数据只能反映异常情况,对于故障的实际原因还需人为判断。
●维修情况
扇形段在维修完成时,都会记录其相应的每个辊子的对中值,只要在符合的范围内,都可视作修复完成。但其中每一个数据的微小差异,在恶劣的工况条件下对在线寿命有明显的影响。所以可预测性不仅需要监控设备运行状态,还需要掌握设备的初始状态,两者相结合才可能实现预测性。
●设备零件寿命
设备是否运行正常,依赖于其零件运行是否正常。而4cc机组从扇形段至辊子,其中的零件数量众多,使用的工况也可不一样,例如0号段浇筑的钢水温度超过1000摄氏度,而E号段的钢坯温度不超过600摄氏度,不同的工况对于零件寿命的影响也是巨大的。
对于一整条流水线而言,不能只考虑单体扇形段的运行情况,要从全局来判断,那么E段的寿命高于0号段,0号段中的结晶器、铜板等寿命就决定整条流水线的单次浇筑寿命长短。
●故障多变
4cc机组在运行过程中,有时仅仅因为长短辊水温异常,就继而导致润滑不完全,进一步加剧辊子转动不同步的情况,最终长短辊轴承滚珠碎裂。从此过程来看,水温异常会进一步导致其他故障发生,甚至影响后续其他设备运行。所以设备故障的形式可能不同,只要有连续因果因素存在,就会发现故障多变,难以精确定位故障源头,进一步对精确预测造成困难。